En este artículo analizaremos las principales novedades que podemos encontrar en el sector de las segadoras y empacadoras, máquinas muy utilizadas en cultivos forrajeros y, en el caso de empacadoras, también en cereales.
F. J. García Ramos. Escuela Politécnica Superior de Huesca. Universidad de Zaragoza.
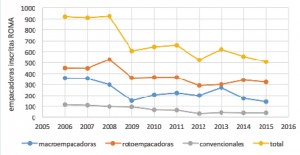
Figura 1. Empacadoras inscritas en el registro de maquinaria agrícola (ROMA) durante los últimos diez años en función de su tipología.
Un primer análisis del mercado de ventas de segadoras y empacadoras, en base a los datos de maquinaria inscrita en los Registros Oficiales de Maquinaria Agrícola (ROMA) de todas las provincias de España durante los últimos diez años (figuras 1 y 2), muestra una evolución descendente en el caso de empacadoras e irregular en el de segadoras.
Centrándonos en primer lugar en las empacadoras, podemos observar como actualmente, las rotoempacadoras (foto 1) y las empacadoras de grandes pacas prismáticas (macroempacadoras, foto 2) son las tipologías más demandadas en nuestras explotaciones, representando aproximadamente el 90% de este tipo de máquinas, quedando el 10% restante para las empacadoras convencionales de pequeñas pacas prismáticas.

Figura 2. Segadoras inscritas en el registro de maquinaria agrícola (ROMA) durante los últimos diez años.
Más en detalle, las rotoempacadoras cuentan con un rango de ventas aproximado entre el 50-60 % y las macroempacadoras entre el 30-40%. La venta de empacadoras ha ido descendiendo hasta situarse en 2015 en 506 máquinas inscritas. Analizando los últimos diez años (figura 1) este descenso ha sido más marcado en el caso de macroempacadoras.
Considerando la distribución geográfica, las rotoempacadoras se concentran de forma mayoritaria en Galicia, Cantabria, Castilla y León y Cataluña, en este caso ligadas a explotaciones forrajeras-ganaderas, mientras que las macroempacadoras tienen mayor presencia en Castilla y León, Castilla-La Mancha, Andalucía y el valle del Ebro, principalmente ligadas a explotaciones cerealistas.
Analizando el mercado de fabricantes, en rotoempacadoras las marcas más demandadas son: Krone, Claas, New Holland y John Deere. En el caso de macroempacadoras destacan: New Holland, Krone, Case IH, Fendt y Claas. Considerando las empacadoras convencionales podemos citar como marcas más vendidas a Welger y John Deere.
En el caso de segadoras (foto 3), la tendencia durante los últimos años ha sido irregular con incrementos y decrementos en el número de máquinas registradas siendo la cifra de máquinas inscritas en 2015 de 351 (figura 2). El promedio de máquinas inscritas durante los últimos diez años ha sido de 441. En lo relativo a fabricantes, destaca la concentración de ventas entre un número reducido de marcas, destacando Kuhn, Krone y Pöttinger, entre las cuales concentran más del 50% del mercado de ventas.
Aunque no existen datos oficiales del número de segadoras inscritas en función de su tipología, actualmente son totalmente mayoritarias las segadoras de discos frente a las segadoras de tambores o con barra de corte tradicional. Podríamos decir, que aproximadamente el 85-90% de las máquinas inscritas corresponderían a segadoras de discos.
Las segadoras se concentran principalmente en las zonas forrajeras y ganaderas, destacando Castilla y León, Galicia, Asturias, Cantabria, País Vasco, Aragón y Cataluña.
Innovaciones técnicas en empacadoras
Las principales novedades técnicas de las empacadoras se han centrado en el aumento de la capacidad de trabajo y en la utilización de equipos combinados de empacado-encintado en el caso de las rotoempacadoras.

Figura 3. Sistema Twinpact de Kuhn para macroempacadoras. Parte superior: sistema tradicional con pistón. Parte inferior: sistema de doble pistón Twinpact.
Analizando en primer lugar las macroempacadoras de pacas prismáticas, la tendencia a poder conseguir pacas de gran densidad continúa. Ya durante 2014 pudimos ver cómo Kuhn desarrolló para su empacadora LSB 1290 iD un sistema de doble pistón, conocido como Twinpact (figura 3), basado en la utilización de un pistón dividido en dos partes (superior e inferior) que comprime la paca en dos pasos diferenciados, de modo que los dos semipistones no golpean a la vez, produciendo así una mayor densidad (hasta el 25% frente a otros equipos convencionales) y sin necesidad de más potencia en el tractor.
Esta tendencia se mantiene y, de forma más reciente, en FIMA 2016, ha destacado como Novedad Técnica Sobresaliente el sistema de regulación automática de la presión de empacado APC (Automatic Pressure Control) de las macroempacadoras Quadrant de Claas. Este sistema está disponible en los modelos Quadrant 5200 y 4200, y fue premiado también en la última edición de Agritechnica, con una medalla de plata.
Se basa en el control adicional de la presión de empacado (además de controlar la presión del marco del canal de compresión) teniendo en cuenta también la calidad del hilo de atado y su carga máxima de trabajo, de forma que la presión de la paca se puede regular para no sobrepasar la resistencia máxima del hilo de atado.
En el caso de las rotoempacadoras, las principales novedades se centran también en el aumento de la capacidad de trabajo con la introducción de mejoras técnicas en los equipos combinados que incluyen en una única máquina los sistemas de empacado y encintado.
Un ejemplo es el sistema Non stop desarrollado por Krone hace unos años incorporado en la rotoempacadora-encintadora Krone Ultima y consistente en una empacadora de cámara variable equipada con una cámara de precompresión en la que el producto puede ser dirigido de forma reversible, bien hacia la cámara de empacado bien hacia el picador situado en la zona de recogida, permitiendo así que la empacadora trabaje en continuo sin necesidad de detenerse en ningún momento y realizar simultáneamente las labores de empacado y encintado.
Figura 4. Proceso de conformación de la paca del sistema FastBale de Vicon: 1) llenado de precámara, 2) paso de la paca a la cámara principal, 3) acabado final de la paca en la cámara principal, 4) alimentación de la precámara para conformar la paca, 5) paso de la paca ya finalizada a la zona de encintado y 6) encintado de la paca.
Como ejemplo similar más reciente, en FIMA 2016 ha sido premiada como Novedad Técnica Sobresaliente la rotoempacadora-encintadora non stop FastBale Vicon (foto 4), que ya fue premiada como máquina del año en SIMA 2015. El sistema FastBale consiste en dotar a la empacadora de dos cámaras de empacado conectadas en serie (precámara y cámara principal) de forma que comparten parte de los rodillos de compactación perimetrales. El objetivo final es poder trabajar de forma continua conformando pacas sin tiempos muertos (figura 4).
Para ello, la primera cámara, que trabaja como una precámara, produce una paca cuyo tamaño es aproximadamente dos tercios del tamaño final. En la precámara se fija una presión de consigna y, una vez alcanzada dicha presión (la paca ocupa en ese momento todo el espacio de la precámara), la paca es transferida a la cámara principal donde continúa el proceso de empacado hasta su tamaño (máximo 1,25 m) y densidad final de modo que el forraje en este caso alimenta directamente a la segunda cámara.
Cuando la paca ha sido finalizada el flujo de forraje (alimentación) pasa de nuevo a la primera cámara para poder comenzar a conformar una nueva paca sin necesidad de detener el proceso de trabajo. En ese mismo instante se aplica una malla a la paca ya conformada que es transferida a una encintadora que se encuentra suspendida en la parte posterior del equipo donde se produce el encintado final de la paca.
Adicionalmente, las novedades técnicas introducidas en las rotoempacadoras han ido ligadas a la evolución de las encintadoras para la conformación de microsilos. En este sentido, en FIMA 2016 ha sido galardonado como Novedad Técnica el sistema de doble bobina e-Twin de Kuhn (foto 5).
Este sistema es utilizado por las encintadoras arrastradas de pacas redondas y mesa giratoria de Kuhn (modelos RW 1410 y RW 1610), y tiene como objetivo disminuir el tiempo necesario para envolver las pacas, aumentando así la capacidad de trabajo. La idea se basa en la utilización de dos rollos de plástico de forma que el plástico de ambos rollos se solapa en dos terceras partes y se pega antes de salir de la unidad de pretensado, obteniendo así una capa doble de forma previa a depositarse sobre la paca. De este modo se consigue un menor tiempo de encintado y una mayor anchura de la capa plástica al llegar a la paca.

Figura 5. Proceso de siega de las segadoras-acondicionadoras. A: barra de corte; B: rodillos acondicionadoes y C: salida del forraje.
Otro ejemplo de aumento de la capacidad de trabajo es el cabezal ProCut de las macroempacadoras de Fendt, presentado en Agritechnica 2015 (foto 6). Este fabricante ha equipado a los modelos 990, 1270, 1290 y 1290 XD con el nuevo cabezal ProCut, que se caracteriza por un rotor de mayor diámetro (650 mm) y mayor velocidad de giro (120 rpm) y con una gran capacidad de picado.
La longitud de corte se puede ajustar desde el terminal para lo que Fendt ha incrementado el número de cuchillas de sus modelos situándolos en 26 cuchillas en los modelos 1270, 1290, 1290 XD y 17 cuchillas en el modelo 990. Se podrían alcanzar longitudes de corte de 43,5 mm. La versatilidad en la longitud de picado también ha mejorado puesto que las cuchillas se pueden situar en dos pistas, con lo cual se puede dividir por la mitad el número de cuchillas que trabajan desde el terminal de la máquina consiguiendo anchuras de corte de 88 mm.
Innovaciones técnicas en segadoras
Quizás la evolución en el sector de las segadoras, al tratarse de máquinas con una mayor sencillez mecánica, no ha sido tan relevante. No obstante, la tendencia es similar, con el objetivo de disponer de equipos con gran capacidad de trabajo, principalmente pensados para grandes explotaciones y empresas de servicios.

Foto 7. Equipo de siega Claas combinado con segadora frontal Disco 3600 FRC y segadora trasera Disco 3600 R.
En base a este hecho, se ha potenciado el desarrollo de las segadoras de discos, con velocidades de trabajo elevadas (de hasta 15 km/h) y con equipos compuestos por barras de corte frontales y traseras (hasta dos traseras y una frontal) de forma que se consiguen anchuras de trabajo muy elevadas, hasta valores en torno a los 10 m. Como ejemplo, la foto 7 muestra un equipo combinado con segadora frontal y trasera, equipadas con acondicionadores de rodillos de goma, muy utilizado en las explotaciones forrajeras del valle del Ebro para la siega y acondicionado de alfalfa.
Durante los últimos años está creciendo ligeramente la presencia de segadoras equipadas con sistemas de acondicionado en la parte posterior de la barra de corte (figura 5), en algunos casos favorecidos por la demanda de esta tecnología por algunas instalaciones de deshidratado industrial. El objetivo de los acondicionadores es producir el aplastamiento o quiebra de los tallos para acelerar el proceso de secado. En este sentido, los fabricantes ofertan acondicionadores de rodillos (foto 8) y acondicionadores de dedos metálicos o de plástico (foto 9). En general, los acondicionadores de rodillos son más adecuados para trabajar con alfalfa y los de dedos para trabajar con hierba.
Como equipamiento habitual este tipo de máquinas incorporan sistemas de seguridad frente a impactos de modo que la máquina gira y vuelve a su posición inicial una vez pasado el obstáculo, sistemas de regulación de la presión ejercida sobre el terreno por el cabezal de siega, discos de corte específicos en función del cultivo a segar, ajuste de la altura de corte, posibilidad de regulación del ángulo de la barra de corte y posibilidad de regulación del sistema de acondicionado. n