Los equipos de aplicación de productos fitosanitarios están diseñados para distribuir una dosis uniforme de producto en el cultivo. Durante los últimos años se han incorporado a este sector y a esta tipología de máquinas numerosos avances tecnológicos, muchos de ellos ligados a la agricultura de precisión. Sin embargo, se han realizado pocos estudios relacionados con el sistema de agitación del depósito, elemento clave para garantizar que la mezcla de las sustancias activas en el caldo es homogénea durante todo el proceso de aplicación.
F.J. García-Ramos, M. Vidal, A. Boné, A. Jiménez. Laboratorio de Maquinaria Agrícola. Escuela Politécnica Superior. Universidad Zaragoza. Campus Huesca.
Los lectores pueden tomar como punto de partida el artículo publicado en el número 407 de Vida Rural (febrero de 2016) en el que nuestro grupo de investigación describía los principales aspectos técnicos de los sistemas de agitación. En este artículo, avanzaremos más en esa línea mostrando cómo afectan los parámetros de regulación de dicho sistema a la calidad de la agitación.
Depósitos y sistemas de agitación
La tipología de depósitos presentes en los equipos de aplicación de productos fitosanitarios es muy diversa. Los tamaños son variables. En el caso de pulverizadores hidráulicos de barra su capacidad varía en función de la tipología: 400 – 1.800 l en equipos suspendidos; 2.400 – 12.000 l en arrastrados; 2.500 – 5.300 l en autopropulsados. Para el caso de pulverizadores hidroneumáticos (atomizadores) estos valores suelen oscilar entre 400 y 4.000 l.
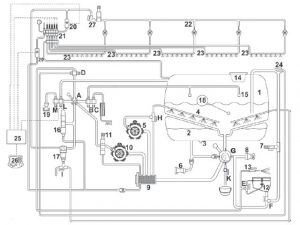
Figura 1. Circuito hidráulico de un pulverizador de barra con sistema de agitación (4) accionado por una bomba específica (5), independiente de la bomba de pulverización. Documentación Amazone.
El depósito representa un volumen significativo dentro de la máquina y su diseño por lo tanto caracteriza la personalidad de la misma. Los fabricantes, durante los últimos años, han optado por diseños agresivos, más aerodinámicos utilizando polietileno de forma mayoritaria.
En lo relativo a componentes, los depósitos van equipados con sistemas de agitación, indicador de nivel, sistema de vaciado, dispositivos de llenado y dispositivos de mezcla. Adicionalmente incorporan depósitos de agua limpia para urgencias en caso de accidentes o limpieza personal, o para limpieza interna de la máquina.
En cuanto al sistema de agitación, su objetivo es mantener la concentración de materia activa homogénea de manera que el fluido que sale por las boquillas tenga la misma cantidad de materia activa por unidad de volumen. Dicho sistema debe ser capaz de agitar el fluido en el interior del depósito, generando un régimen turbulento, para garantizar una correcta mezcla del producto.
Técnicamente, existen tres modalidades de agitadores (hidráulicos, mecánicos y mecánico-hidráulicos) si bien la mayoría de los equipos disponen del sistema de agitación hidráulico, por lo que nos centraremos en dicho sistema.
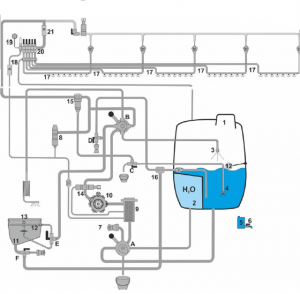
Figura 2. Circuito hidráulico de un pulverizador de barra con sistema de agitación (4) accionado de forma simultánea por la bomba del sistema de pulverización (10). Documentación Amazone.
Los agitadores hidráulicos se basan en la utilización de boquillas ubicadas en la zona inferior del depósito que inyectan fluido en el mismo generando el movimiento del agua en su interior y facilitando así la agitación. Como norma habitual, el caudal del sistema de agitación se debe situar entre el 5 y el 10% del volumen del depósito. El caudal aportado por el sistema de agitación es suministrado bien por una bomba de agitación específica (figura 1) independiente de la bomba de pulverización (caso habitual en pulverizadores con un número de boquillas elevado), bien por la propia bomba de pulverización, la misma por lo tanto que aporta fluido a las boquillas de pulverización del cultivo (figura 2).
En este caso, la bomba debe estar dimensionada para aportar, además del caudal requerido por las boquillas de aplicación, el caudal requerido por el sistema de agitación. Los caudales de las bombas de pulverización son muy variables en función de las características técnicas de los equipos. En el caso de pulverizadores hidroneumáticos (atomizadores) oscilan entre 50 y 280 l/min, utilizando principalmente bombas de pistones y de diafragma con presiones de trabajo habituales entre 5 y 15 bar.
En el caso de pulverizadores hidráulicos de barra los caudales son similares, con presiones de trabajo recomendadas normalmente por debajo de 5 bar y bombas de pistones, diafragma o centrífugas, estas últimas para el caso de grandes caudales, ligadas a barras de anchuras de trabajo elevadas.
En el sistema de agitación se suelen utilizar boquillas de tipo Venturi (figura 3) para aumentar el caudal de fluido movido por las mismas, de forma que el caudal final movido se sitúa en torno a 4 o 5 veces el caudal de entrada en la boquilla (sin Venturi) ya que el sistema de alimentación Venturi arrastra fluido existente en el depósito además del introducido por la boquilla.
Como ejemplo, el cuadro I muestra los caudales aportados por una boquilla de agitación comercial de tipología Venturi a diferentes presiones de trabajo. Se puede diferenciar el caudal específico de la boquilla (caudal A) y el incremento de caudal (caudal B) que se consigue con el efecto Venturi al incorporar al flujo caudal existente en el propio depósito, consiguiendo por lo tanto un flujo de líquido total A+B.
Parámetros que condicionan el funcionamiento del sistema de agitación
En el caso de sistemas de agitación hidráulicos, los principales parámetros relacionados con el correcto funcionamiento del sistema de agitación son aquellos que condicionan la generación de un régimen turbulento en el fluido del depósito. Básicamente este hecho se consigue en función del número de boquillas, de su distribución/posición en el interior del depósito y de la presión de trabajo del circuito, ya que ésta condiciona el caudal y la velocidad de salida del fluido.
Adicionalmente, hay otro parámetro que condiciona el funcionamiento y es el nivel de llenado del depósito, ya que, como es lógico, la capacidad de agitación es menor cuando el depósito se encuentra a su máximo volumen de llenado. No obstante, este parámetro no es objeto de regulación.
El principal problema al que se enfrenta un fabricante o un usuario es, por lo tanto, cómo valorar el correcto funcionamiento del sistema de agitación.
Como ejemplo, la obligatoria inspección de equipos fitosanitarios en uso (basada en la norma UNE-EN ISO 16122) actualmente sólo especifica que, para valorar el correcto funcionamiento de la agitación, la inspección del depósito será visual, con el depósito lleno hasta la mitad de su capacidad nominal, con la bomba funcionando al régimen nominal recomendado por el fabricante, y con el pulverizador equipado con las boquillas de mayor caudal trabajando a la presión máxima de trabajo recomendada.
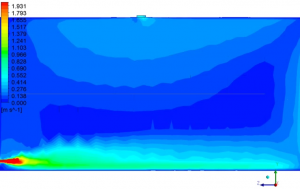
Figura 4.Mapa de velocidades en el interior de un depósito obtenido mediante dinámica de fluidos computacional con una boquilla del sistema de agitación ubicada en la parte inferior izquierda del depósito.
En estas condiciones, la norma se limita a detallar que se comprobará que se mantiene un flujo constante y uniforme en todas las boquillas, mientras que se observa un movimiento del líquido en el interior del depósito suficiente para garantizar la agitación del mismo. Por lo tanto, queda patente que esta inspección no es un método riguroso para poder constatar de forma clara el funcionamiento del sistema de agitación, ya que es un método subjetivo ligado a la interpretación visual.
Como alternativa, se puede aplicar la norma ISO 5682-2: 1997, Equipos para tratamientos fitosanitarios. Pulverizadores agrícolas. Parte 2: Métodos de ensayo para pulverizadores hidráulicos.
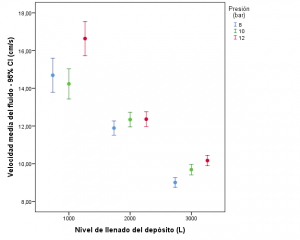
Figura 5. Velocidades medias en el interior de un depósito con tres niveles de llenado (1.000, 2.000 y 3.000 l) y tres presiones de trabajo (8, 10 y 12 bar).
Esta norma se basa en la medida de la concentración de materia activa en el caldo de pulverización. Para ello, tras introducir un trazador a una determinada concentración en el depósito, se toman muestras de producto en diferentes condiciones (interior del depósito y boquillas de pulverización) y se analiza su concentración para posteriormente comparar la uniformidad en los valores de concentración de materia activa en los diferentes puntos de muestreo y su desviación frente a la concentración teórica. Como trazador se utiliza oxicloruro de cobre.
Esta metodología aporta datos que permiten valorar de forma rigurosa el correcto funcionamiento del sistema de agitación, pero lógicamente con un coste elevado tanto de tiempo como de medios técnicos.
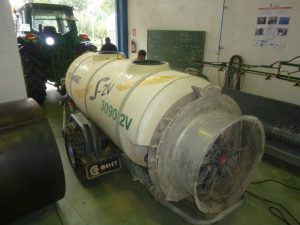
Foto 2. Depósito de 3.000 l del pulverizador hidroneumático donde se realizaron ensayos de medida de velocidad de fluido y concentración de materia activa.
Como alternativa, se puede recurrir a la medida de velocidades (foto 1) en el interior del depósito y establecer umbrales mínimos de velocidad que garantizan una buena concentración, mediante comparación con medidas experimentales de concentración. Así, los datos de medidas empíricas de concentración obtenidos para una configuración del sistema de agitación (presión del circuito, número de boquillas activas y nivel de llenado del depósito) se pueden correlacionar con velocidades del fluido y extrapolar dichas conclusiones a diferentes configuraciones del sistema de agitación reduciendo de este modo la carga experimental.
Finalmente, estos datos (velocidades y concentración) también se pueden usar para validar modelos de simulación desarrollados en ordenador mediante la técnica de la dinámica de fluidos computacional (figura 4), metodología idónea para que los fabricantes de pulverizadores puedan abordar de forma más fiable la fase de diseño previa al desarrollo del primer prototipo.
A continuación explicamos el efecto sobre la calidad de agitación de los diferentes parámetros de regulación para que el lector pueda valorar su importancia y por lo tanto, la importancia de un buen diseño del sistema de agitación.
Nivel de llenado del depósito y presión de trabajo
El nivel de llenado dentro del depósito afecta de forma significativa a la velocidad que alcanza el fluido en el mismo. En este sentido, la velocidad del fluido disminuye significativamente cuando aumenta la cantidad de caldo en el depósito. Este hecho pone de manifiesto que los ensayos del sistema de agitación se deberían realizar en las condiciones más desfavorables, ligadas a mayor cantidad de caldo en el depósito.
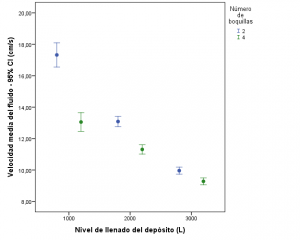
Figura 6. Velocidades medias en el interior de un depósito con dos o cuatro boquillas activas y tres niveles de llenado (1.000, 2.000 y 3.000 l). En el caso de cuatro boquillas activas los flujos de las boquillas se enfrentaban debido a su ubicación en caras opuestas del depósito.
Como ejemplo, la figura 5, obtenida a partir de ensayos realizados por nuestro grupo de investigación para un pulverizador hidroneumático comercial (foto 2), muestra la velocidad media del fluido en el interior de un depósito con capacidad de 3000 l, considerando 32 puntos de medida ubicados en diferentes posiciones para tres niveles de llenado del mismo (1.000, 2.000 y 3.000 litros), trabajando a tres presiones de trabajo diferentes (8, 10 y 12 bar).
El depósito estaba equipado con un sistema de agitación de hasta cuatro boquillas Venturi. Como se puede apreciar, el rango de velocidades medias fue menor cuanto mayor fue el volumen de agua en el depósito y varió entre 9 y 17 cm/s aproximadamente. Con este rango de velocidades se consiguió una mezcla homogénea de producto.
En lo referente a la presión del circuito que alimenta a las boquillas del sistema de agitación, la figura 5 muestra cómo, en términos generales, la velocidad del fluido en diferentes zonas del depósito aumenta con la presión de trabajo.
Otro aspecto que afecta de forma directa la eficacia del sistema de agitación es la ubicación física de las boquillas. Se debe evitar situarlas enfrentadas entre sí para evitar que los flujos se contrarresten, hecho que produce una reducción significativa de la velocidad del fluido.
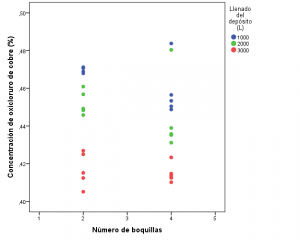
Figura 7. Concentración de oxicloruro de cobre en el interior del depósito en función del nivel de llenado (1.000, 2.000 y 3.000 l) y el número de boquillas activas.
Como ejemplo, la figura 6 muestra el depósito analizado con anterioridad trabajando en dos situaciones, con dos boquillas activas o con cuatro, pero en este segundo caso, los flujos estaban enfrentados entre sí por parejas de boquillas cuando las cuatro boquillas actuaban a la vez, no así cuando sólo actuaban dos. Se puede observar cómo la concentración de producto en el interior del depósito fue menor para el caso de cuatro boquillas, y además se obtuvieron velocidades del fluido menores (figura 7).
Del mismo modo, la concentración se redujo cuando el depósito tenía más cantidad de líquido y, por lo tanto, menores velocidades como refleja la figura 5. Este hecho pone de manifiesto cómo una mayor velocidad mejora la mezcla del producto evitando su deposición en el fondo del depósito.
Conclusión
El diseño de los sistemas de agitación hidráulicos de los equipos de aplicación de productos fitosanitarios debe evitar la ubicación de las boquillas en posiciones enfrentadas dentro del depósito, con el objetivo de conseguir las máximas velocidades del flujo en el interior del mismo. Velocidades elevadas del fluido en el interior del depósito consiguen una mejor mezcla de materia activa. Cuanto mayor sea la presión de trabajo de las boquillas y por lo tanto el caudal aportado, mejor será la agitación. Las condiciones de agitación más exigentes se producen con los depósitos a su máxima capacidad por lo que es en esa situación cuando deben ser ensayados y validados.
La medida de velocidades en el interior del depósito y la modelización CFD se muestran como claras alternativas a los ensayos tradicionales basados en la medida de concentraciones de producto fitosanitario detallados en la norma ISO 5682-2.