La tecnología de pulverización de productos fitosanitarios, basada en la utilización de circuitos hidráulicos y, en su caso, sistemas neumáticos, posibilita que este tipo de máquinas estén en constante evolución mediante la implementación de innovaciones dirigidas a controlar al máximo las dosis y a disminuir la deriva o pérdida de producto durante la aplicación.
F. J. García Ramos, A. Jiménez, M. Vidal, A. Boné. Escuela Politécnica Superior. Universidad Zaragoza-Campus Huesca.
Nos centraremos en las dos grandes tipologías de equipos de aplicación, pulverizadores hidráulicos de barra para cultivos extensivos y pulverizadores hidroneumáticos (atomizadores) para frutales y viñedos, que representan aproximadamente el 95% de los equipos presentes en nuestras explotaciones.
De forma común, todos ellos incorporan sistemas de caudal proporcional al avance, que garantizan que la dosis aplicada (l/ha) se mantiene constante independientemente de la velocidad de avance de la máquina. También es habitual la utilización de boquillas de baja deriva que amplían las posibilidades de trabajo en campo en condiciones desfavorables de viento.
Analizando, en primer lugar, los equipos de barra, las principales tendencias/características de los equipos actuales son anchuras de trabajo elevadas y tecnología de control de la pulverización en diferentes zonas de la barra (control individual de boquillas, control de tramos, etc.).
En el caso de los atomizadores utilizados en frutales, los fabricantes han centrado sus esfuerzos en implementar sistemas que controlen al máximo la trayectoria del producto para evitar las pérdidas por deriva. En este sentido, durante los últimos años, se han mejorado los sistemas neumáticos para poder adaptar el caudal de aire a la vegetación real del cultivo, se ha trabajado en la adaptación del arco de boquillas a la geometría del cultivo y ya es habitual la utilización de sensores (normalmente acústicos) para detectar la presencia o no de cultivo en plantaciones aisladas (olivo, almendro, etc.) que permiten implementar sistemas on-off para ahorrar dosis de producto y evitar contaminación ambiental.
Innovaciones en pulverizadores de barra
La actual tendencia al aumento de la capacidad de trabajo de las barras de pulverización (foto 1) está provocando que los fabricantes optimicen al máximo el diseño de las mismas para conseguir que, con elevadas anchuras de trabajo, se mantenga una estabilidad óptima de la barra, con un paralelismo adecuado entre la superficie del cultivo y la barra, garantizando así una distribución uniforme del producto. Para ello, los fabricantes implementan barras con diseños que aporten una adecuada rigidez, con materiales ligeros como aluminio (foto 2), fibra de carbono (foto 3) y con sistemas automáticos de corrección del paralelismo entre barra y cultivo.
Hasta ahora ha sido habitual el desarrollo de sistemas para el control de la posición vertical de la barra basados en la utilización de sensores de ultrasonidos (foto 4) capaces de chequear las condiciones de paralelismo con el cultivo y corregir en su caso la inclinación de la barra mediante sistemas hidráulicos. Como ejemplos podemos citar el sistema DistanceControl de Amazone, el sistema AutoHeight de Hardi, o el sistema BoomTrac de John Deere.
Un paso más en esta línea lo constituyen los sistemas de control del movimiento horizontal de la barra en la dirección de avance del tractor. Como ejemplo de esta nueva tecnología, Amazone ha implementado el sistema SwingStop (figura 1), el cual utiliza acelerómetros colocados en los extremos de la barra que miden el movimiento horizontal de la misma. En caso de movimiento excesivo un sistema hidráulico permite corregir la posición horizontal de la barra.
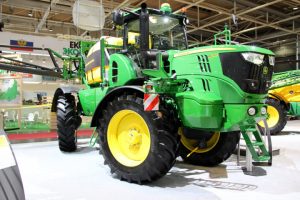
Foto 3. Pulverizador hidráulico autopropulsado con barra de fibra de carbono. Documentación John Deere.
Por otro lado, la tendencia a utilizar materiales ligeros en las barras se va consolidando. Ya es habitual la utilización de aluminio y es posible que pronto veamos, de forma más generalizada y no sólo para casos puntuales, la fibra de carbono en barras con grandes anchuras de trabajo. De hecho, John Deere (después de trabajar bajo un convenio desde 2015) ha adquirido en 2018 a la empresa King Agro, de capital argentino y ubicada en Picassent (Valencia), la cual es especialista en la fabricación de componentes con fibra de carbono.
Es ya una realidad extendida en la mayoría de los fabricantes la tecnología de cierre automático de sectores, y la de cierre individual de boquillas, basada en la utilización de sistemas de posicionamiento GPS ligados a la apertura y cierre de válvulas ubicadas en el circuito hidráulico de la máquina. El objetivo final es evitar solapamientos entre pasadas y controlar con precisión los tratamientos en los bordes de parcela, o en parcelas con geometrías irregulares.
Otras tendencias, todavía por consolidar, son el diseño de máquinas polivalentes, que pueden ser útiles para ciertos tipos de explotaciones. Un ejemplo es el sistema Awasulf del fabricante español General (foto 5), que introduce una cortina de aire en una barra de pulverización, tecnología ya desarrollada hace años, pero que presenta la novedad de que puede aplicar productos sólidos y líquidos de forma independiente o de forma conjunta. Se trata de una máquina pensada principalmente para cultivos hortícolas.
Innovaciones en atomizadores
Los fabricantes siguen avanzando en controlar al máximo el caudal de aire del ventilador y para ello han desarrollado sistemas que modifican de forma automática el giro de los álabes y, por otro lado, pueden modificar la anchura de salida del aire jugando así con la velocidad y el alcance de las gotas.
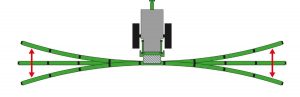
Figura 1. Sistema Swingstop de Amazone para el control del movimiento horizontal de la barra de pulverización. Documentación Amazone.
Un ejemplo de innovación tecnológica es el atomizador Futur H3O desarrollado por el fabricante español Fede que incorpora ya desde 2016 un sistema de calibración automático del aire. El sistema de control dispone de modelos para la estimación del caudal requerido basados en el volumen de vegetación (TRV, tree row volume), la velocidad de avance, el marco de plantación, el tipo de cultivo y el tipo de tratamiento que se realiza. A partir de dichos datos se estiman la dosis recomendada y el volumen de aire para lo cual el equipo dispone de un sistema CPA de aplicación de dosis proporcional al avance y un sistema de control de los álabes del ventilador.
Tecnología de boquillas
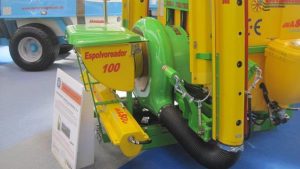
Foto 5. Sistema Awasulf de General para la aplicación de producto líquido y sólido con el mismo equipo.
Las boquillas siguen siendo una parte fundamental de los pulverizadores ya que inciden de forma significativa en la calidad del tratamiento. Los fabricantes optimizan el diseño en dos líneas: producir boquillas de baja deriva que permitan trabajar en condiciones difíciles e implementar tecnología que controla individualmente el trabajo de cada boquilla. Lógicamente, estos desarrollos se pueden incorporar en máquinas ya existentes de forma sencilla y rápida.
Para el control individual del funcionamiento de la boquilla existen dos opciones, la utilización de boquillas de pulsos (PWM) y la utilización de válvulas de cierre/apertura individual de cada boquilla (o de un tramo de boquillas en su defecto).
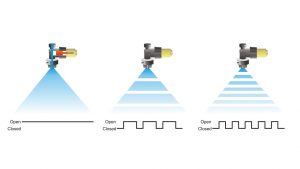
Figura 2. Válvulas para el control individual de las boquillas utilizadas en tecnología WPM. Izquierda: Válvula abierta de forma continua. Centro y derecha: válvula abriéndose y cerrándose con diferentes frecuencias de trabajo.
Las boquillas de modulación de la anchura de pulso (PWM – pulse width modulation, figura 2) permiten ajustar electrónicamente y de forma independiente, mediante la apertura y cierre de la boquilla a alta frecuencia, la dosis de caldo aportada por cada boquilla sin modificar la presión de trabajo del circuito hidráulico consiguiendo de esta forma caudales diferenciados en boquillas de la misma barra.
Las válvulas electrónicas se pueden incorporar de forma sencilla junto a las boquillas y permiten realizar encendidos y apagados individuales de cada boquilla, permitiendo el control total de la pulverización. Un ejemplo es la válvula ESV (electrical stop valve) desarrollada por Lechler.
Gestión de la información
El control de los parámetros de trabajo de la máquina es otra tendencia que ha venido para quedarse. La adquisición de los datos relativos al funcionamiento de los equipos, ligada a su transmisión a la “nube”, es una práctica habitual en tractores y cosechadoras que ahora está comenzando a implementarse en los aperos y máquinas accionadas.
Como ejemplo, en la pasada FIMA, Pulverizadores Fede fue premiada por su sistema Smartomizador (foto 6) que permite una conexión directa entre el técnico, la máquina y el operario, teniendo en todo momento información sobre la aplicación a tiempo real y almacenando los datos del tratamiento en una plataforma digital.
Nuevas estrategias de tratamientos
La cada vez más exigente legislación medioambiental está provocando que los fabricantes mejoren al máximo sus equipos para tener un control máximo del producto aplicado y evitar derivas y contaminaciones. Por otro lado, también está provocando el diseño de nuevos sistemas que eviten el uso de productos químicos. En este sentido, para el caso de eliminación de malas hierbas en plantaciones frutales y viñedo, es cada vez más habitual la utilización de máquinas que eliminan mecánicamente las malas hierbas, como los equipos intercepas en viñedo.
Como ejemplo de innovación tecnológica para eliminar malas hierbas, podemos citar el equipo Grasskiller (foto 7) del fabricante italiano Caffini, que dispone de uno o dos cabezales para trabajar en la línea de viñedo o de frutales. Dichos cabezales aplican agua a muy alta presión (1.000 bar) sobre la línea de plantación para eliminar las malas hierbas y disponen de un cabezal basculante para evitar los troncos. Esta tecnología, está basada en la utilización de bombas de alta presión procedentes del sector de la maquinaria de corte de piedra. El consumo aproximado de agua es de 33 cl por metro lineal.